Custom Rotational Molding Tooling
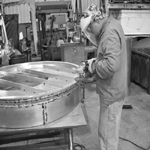
Rotational Molding Tooling, is one of the integral intial capital investments that is required to produce a Rotationally Molded Product. Rotational Molding tooling can be manufactured thru various processes such as casted aluminum tooling, fabricated aluminum tooling, fabricated steel or even fabricated stainless steel. There are also a number of cast bronze molds and machined tools as well. Todays leading Custom Rotational Molding houses are typically forced to have in house tooling centers and repair shops to keep production going on running tools and consistently growing new customers with new tooling. However, a number of rotomolding suppliers do not offer in house rotational mold tooling maintenance, nor do they build tooling in house. Many of them will even elect to risk their reputations and quality with low quality Chinese tooling. Therefore when your tooling cracks, frame work breaks or the parting line gets damaged, not only are you out of production, you could be out of production for months! As they will have to send your tooling out to another shop to fix. Costing you loss of production, loss of sales and ultimately loss of profits! Don't risk your business or your customer relationships to such! They prices for Rotomolding tools are generally very competitve amongst most quality molders, yet some still risk their business on poor tooling with numerous issues! Rotomolding tooling is generally no different, you get what you pay for!
![]() A Customer sent this mold in from a competitor, the competitor stated that the mold has rusting issues- notice that even after being shipped across the country, it still had snow covering it ! |
![]() |
![]() |
Refurbishing Existing Rotational Mold Tooling
When a leading Custom Rotational Molding Company, like Granger Plastics inherits a tool from either another rotational molding company or maybe the tooling has sat dormant for years, Granger Plastics can get your tooling fixed and into production-PROPERLY!
![]() |
![]() |
Sometimes when a customer runs into an issue with their current supplier or maybe things just change directions, they select Granger Plastics as their new molding supplier, one of the first things Granger will do is bring the tooling in for an evaluation to see how the tooling lines up against the product.
New Rotational Mold Tooling
Typically the intitial investment of tooling is one of the major hurdles of launching a new plastic product. It is often the the "make or break decision" when it comes to many rotational molding opportunities, as a number of interested parties fail to realize the capital requirements of having the necessary tooling to produce the products or components. However, there is still great deal of American entrepeneurialship spirit that continues to develop new ideas, new concepts and products, which involve new containers, tanks, etc. These industry leaders often continue to have their innovations produced by the same leading design team who resolved any design or mechanical design issues and have often had their tooling fabricated with the same high quality rotational molding company that will end up being their long term partner in rotational molding, Granger Plastics.
![]() |
![]() |
![]() |
-
Rotationally Molded Products being produced with Granger Plastics Tooling
Granger ISS Tornado Storm Shelter
One of the leading Fabricated Aluminum Rotational Molds in the World! The Granger ISS consists of a number of different fabicated aluminum tools, all built right here in America, at Granger Plastics! In the Granger ISS Tornado Shelter tooling development, costs for all of the tools, research and modifications, the costing of the tooling alone is approximately $750,000 USD complete. Watch the video's below, the video on the left will show the Granger ISS Tornado Shelter goingt thru the manufacturing process, while the video on the right is the FEMA 320 and FEMA 361 testing on the Granger ISS Door (another rotomolded tool built by Granger Plastics) that shows the same door meets or exceeds FEMA 320 and FEMA 361 standards. Typically, a company would utlize a new door to ensure the passing of the second test. Grangers commitment to safety allows the Granger ISS do to be durable enough to pass an above ground safe room debris impact test!
On top of the thousands of hours of research, design and study for the storm shelter, Granger Plastics also practices a number of philosphies of Dr. W. Edwards Deming. His philosophy that by adapting appropriate principles of management, organizations can increase quality and simultaneously reduce costs (by reducing waste, rework, staff attrition and litigation while increasing customer loyalty.) The key is to practice continual improvement and think of manufacturing as a system, not as bits and pieces"
Do other Storm Shelter manufacturers uphold this level of quality standards? Do many, if any existing Custom Rotational Molding companys have this level of quality and ability?